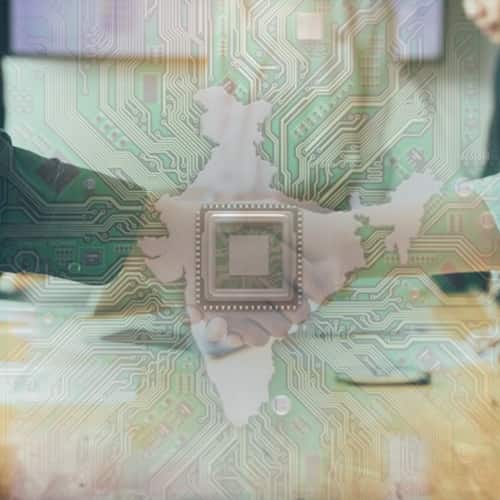
From early 2021, the automotive industry worldwide has been facing a serious shortage of chips. Researchers at the Indian Institute of Science (IISc) have been collaborating with a semiconductor foundry under the IMPRINT program of the Government of India, which could provide a solution to address this issue. The IISc team embarked upon developing an indigenous technology platform for manufacturing automotive (analog) chips to be used for commercial and strategic applications.
Automotive chips are different from the conventional processor chips used in devices such as smartphones and laptops. An automotive chip (also referred to as a power ASIC) needs to handle various tasks simultaneously, including instrumentation, sensing and control of various electro-mechanical parts. The electrical interface to these parts operates at higher voltages (5V-80V) compared to a processor chip, which only requires a low voltage switch or transistor (0.9V-1.8V).
Automotive chips require high-voltage switches or transistors built onto the chip. These transistors are called Laterally Diffused MOS (LDMOS). Silicon LDMOS devices are a type of field-effect transistors which can operate at much higher voltages than regular transistors. They can also be integrated with billions of other transistors inside a chip. This requirement is also particularly important for space and defense applications.
Developing a technology platform that can offer the wide range of capability required by automotive chips has always been a challenge for the industry and can take 5-6 years, unlike the processor technology platform which typically takes about one-and-a-half to two years. However, this extra time investment can pay off in terms of a significantly lower obsolescence rate—such chip technologies can last for 15-20 years without having to be replaced.
The IISc team and its foundry partner have been working on developing a range of LDMOS devices (from 10V to 80V) with characteristics matching current industry offerings. The collaborative effort has led to the development of a robust high voltage automotive technology platform.
Technology platforms available in the industry have enabled the capability of developing circuits that can handle voltages ranging from 7V to 80V, significantly increasing the earlier capabilities of domestic partners of 3.3V. Extending this portfolio to 80V by importing technology would have cost tens of millions of USD. This collaborative effort has augmented the baseline process and enabled the development of devices capable of operating at 80V, at a cost of less than 0.5 million USD.
Prof Mayank Shrivastava (Department of Electronic Systems Engineering) who led the project from IISc, said, “IISc and its partners worked pretty much like an industrial R&D team and handled the fundamental issues differently, which industry usually handles empirically (by trial-and-error). For example, we could delve deeper into some fundamental issues related to these devices, like Quasi-Saturation behaviour, which hasn’t been completely understood/solved in the past 40+ years. Thanks to the IMPRINT programme for enabling such a development, which is turning out to be a win-win for IISc and its foundry partner. These LDMOS devices can now become standard offerings (like any other industry), which will help our foundry partner develop a range of VLSI products in-house. Besides, the technology/knowhow can be transferred to other semiconductor foundries that want to scale up their process from baseline CMOS to an automotive process.”
See What’s Next in Tech With the Fast Forward Newsletter
Tweets From @varindiamag
Nothing to see here - yet
When they Tweet, their Tweets will show up here.