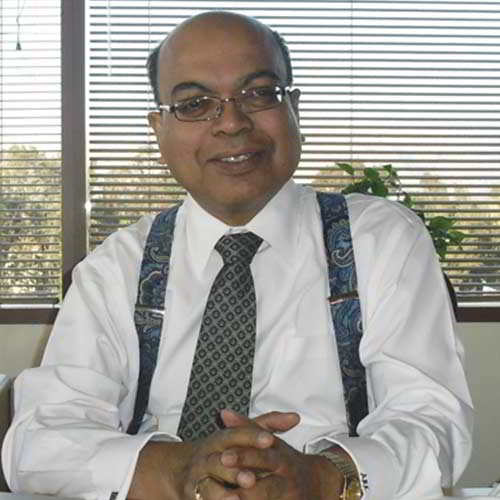
Asoke K Laha, President & CEO of Interra Information Technologies
India has been no exception to the current global shortages of semiconductors. The truth is that it would affect directly or indirectly, the whole population of the world close to 7 billion.
You may possibly ask why? It is quite natural. Let me spell out some of the critical use of semiconductors to illustrate that it has become inseparable with human civilization now. Semiconductors are an essential component for all electronic devices. An estimate indicates that globally one hundred billion semiconductors are used daily in various sectors including artificial intelligence, clean energy, communication, mobile phones, computing, energy, healthcare, Internet of Things and of course, manufacturing of military equipment and aerospace. Its uses are expanding across the world from city planning to smart cities to education. For a country like India, it is estimated that the use of semiconductors is poised to increase manifold with the setting up of over hundred smart cities and focus on automation.
Dynamics around semiconductors is quite complex. The semiconductor industry always depends on four factors for its growth. They are global GDP growth; growth in the IC manufacturing capacity; supply side economics, that is the number of units produced; and of course, average selling prices. This would mean that a fall in global GDP will shrink the demand profile of semiconductors. But this time around the conventional economic theory has lost its relevance. The global GDP in 2020 has fallen 4.4 percent heralding a severe recession in multiple fields. This should have reduced the demand for chips. But the demand remained strong despite the fall in the global GDP. The semiconductor industry had curiously grown by 7.3 percent. That may sound a bit surprising, but it is a fact. The reason is higher growth of electronic devices including mobile phones, e-retail facilities etc. for transacting businesses, when physical contacts were restricted or mandated against and e-transactions were the new normal. That trend is not going to disappear. Rather it may get intensified as the world has recognized the advantages of faceless transactions and the speed in which it can be done across the continents in a split of a second. That is why we hear more about Bitcoins, electronic currency etc.
Let’s look at the production of some of the leading semiconductor units across the world. Companies have seen significant growth in the first quarter of 2021 despite higher prices. In fact, there were massive shortages of semiconductors reported across the world. Samsung reported a growth of 25 per cent. Curiously the only company reported contraction in production was Intel, the largest supplier. Its production was down by 4 percent. The global GDP is set to increase by 5.2 percent in 2021. The top countries where the recovery is going to be strong are India, China, Euro Zone and the US. This will push up the demand for semiconductors. The recovery will be strong in Europe and the UK partly because they, with their exposure to automotive and industrial sectors, suffered the worst with GDP contractions in 2020. That would mean demand and prices for semiconductors are set to increase not for this year, but also for following years, since the demand for electronics devices would register a quantum rise in the coming years.
Who rules the roost in semiconductors? Taiwan is a leading player in chip making. As shortages for the chips are growing, countries like the US and Germany are reaching out to Taiwan to meet their increasing demand. There can be two reasons for shortages. One, the Covid-19, which jacked up the demand for electronic devices and the other was the trade war between the US and China, which to a great extent cut off the supply from China for meeting chip requirements. According to reliable data, a whopping more than 60% of total global foundry revenue last year came from Taiwan.
The chip giant accounted for 54% of total foundry revenue globally last year. Equally significant is the complex nature of chip production. The ecosystem involves a complex network of firms that design and companies that provide technology, machinery materials including components. For instance, TSMC focuses only on manufacturing. It depends on raw materials and components from other companies for chip making. Why is its market share going up? It is because it has under it arms some of the most advanced chips.
This expanded collaboration will benefit semiconductor designers and manufacturers to make chips smaller and better. Currently, TSMC and its South Korean rival Samsung are the only foundries capable of manufacturing the most advanced 5-nanometer chips. TSMC is already gearing up for the next-generation 3-nanometer chips that may start production in 2022.
In a landscape characterized by shortages, some countries like China are planning to increase their own semiconductor production. Countries are aiming to be self-reliant in the field in order to lessen dependence on countries like Taiwan and China. But there have been polemics that confront them. China’s largest chip manufacturing company Semiconductor Manufacturing International Corporation (SMIC), has been blacklisted by the Trump administration categorizing the company under the entity list. That limits the company’s access to technology and machinery that it needs. SMIC ranks the fifth largest semiconductor foundry globally by revenue in 2020. That is, the Chinese firm is a few notches below TSMC and UMC, South Korea’s Samsung, and Global Foundries in the U.S. That situation may continue for some time since SMIC has been cut off, at least for the moment, from acquiring the really cutting-edge equipment it needs from ASML, a Dutch company, at the instance of the earlier Trump Administration. The Dutch company (ASML) makes the so-called extreme ultraviolet lithography equipment that is used to produce the most advanced chips similar to those manufactured by TSMC and Samsung. Experts feel that even if SMIC gets access to ASML’s equipment, it would take years to start producing high-end chips in large quantities. Till that time, the Taiwanese and the South Korean Samsung will have their field days dominating the world market. That is the polemics of the semiconductors, that prompted me to choose the subject for this month’s column.
There are predictions that the global semiconductor shortage will continue for some time. Gartner predicts that through the 2Q22 or 4Q22, there will be shortages. This would lead foundries increasing wafer prices, which in turn will lead to chip companies increasing device prices. Coupled with other capacity constraints and shortages for items like substrates, wire bonding, passives, materials, and equipment for testing, there will be bottlenecks beyond Fabs. Gartner provided a series of recommendations to chip buyers one of which was to join together with other chip customers and form unions to be able to approach chip suppliers and foundries with increased leverage. Another was to pre-pay for products or to invest in suppliers to try and gain guarantees of long-term supply.
Semiconductor manufacturing requires high investment and there is no such facility in India as of now. The investment required to set up a FAB can range from US$3 billion to US$6 billion, depending on wafer capacity of the FAB. India is highly reliant on imports to meet the country's semiconductor requirements. Recently, over twenty semiconductor manufacturing and design businesses in the high-end, display, and specialty fabrication segments have submitted expressions of interest (EOIs) to establish production facilities in India. But we may have to wait for a longer time to know how and when such facilities will roll out their production.
Recently, some countries with a semiconductor manufacturing base have stock piled the chips for meeting their own requirements, seriously affecting the global supply chain. The Indian government should take cognizance of this situation and work towards gaining a foothold in semiconductor manufacturing and become self-reliant.
India should build a basic ecosystem for semiconductor manufacturing. First and foremost, there is the need for semiconductor manufacturing facilities to have a huge uninterrupted power supply. Additionally, semiconductor Fab facilities are also water intensive. It may require more than five million gallons of ultra-pure water per day. To generate this much pure water, one requires at least eight million gallons of city water per day.
India imports solar cells and modules from other countries and this situation needs to be reversed by manufacturing purified silicon within the country. India has huge reserves of silica minerals required for making silicon wafers.
All major global semiconductor companies have their fabless Intellectual Property (IP) and System-on-Chip (SoC) design houses in India. Some estimates predict that the Indian semiconductor design market is expected to reach close to US$8 billion by the end of 2021.
Yes, India has the potential across various disciplines involved in chip making. But the fact is that we lack the capability. One factor, I feel, is that none of the major Indian companies are investing in the electronics sector. It is high time India motivates bigger companies to invest in Foundry because of the higher investment required. That holds the pathway to India making baby steps in the Fab. Otherwise, it would remain as a pipedream. A lot of planning and careful execution is needed in this regard. Are we ready to take on the challenge?
See What’s Next in Tech With the Fast Forward Newsletter
Tweets From @varindiamag
Nothing to see here - yet
When they Tweet, their Tweets will show up here.